Troy Whitman is a seasoned sales professional with over 20 years of experience in building relationships, solving challenges, and driving results. As a key part of the BID Canada team, Troy works closely with clients to deliver tailored solutions in the material handling industry. From belt conveyors to screws and bucket elevators, Troy’s expertise ensures that customers get the right products and support to keep their operations running smoothly.
Troy’s success stems from his ability to spot opportunities and stay ahead of industry trends. Certified by the Canadian Professional Sales Association (CPSA) and having completed Northwestern Kellogg’s Mastering Sales program, he brings a unique mix of formal training and hands-on experience to every project. He’s passionate about finding practical, effective solutions while keeping things straightforward and results-focused.
At BID Canada, Troy is all about collaboration. Whether it’s working with customers to solve specific challenges or supporting his team to meet their goals, he knows that success comes from working together. His approachable style and commitment to building strong relationships make him a trusted partner in every interaction.
When he’s not on the job, Troy keeps busy coaching hockey, where he instills values of teamwork and discipline in young athletes. He’s also an avid traveler and outdoors enthusiast who’s always up for a new adventure. Whether at work or play, Troy brings the same energy, curiosity, and problem-solving mindset to everything he does, making him a valuable part of the BID Canada and McDonough family.
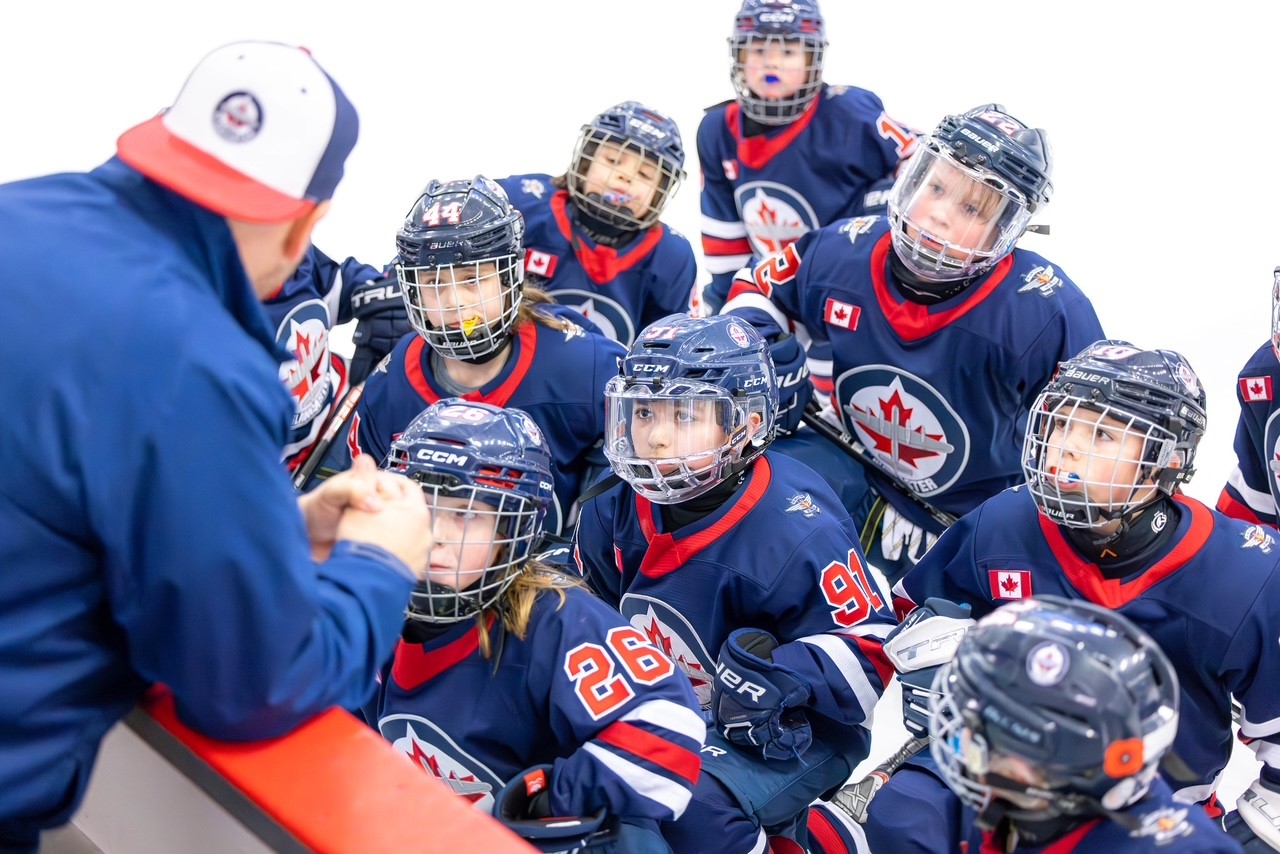
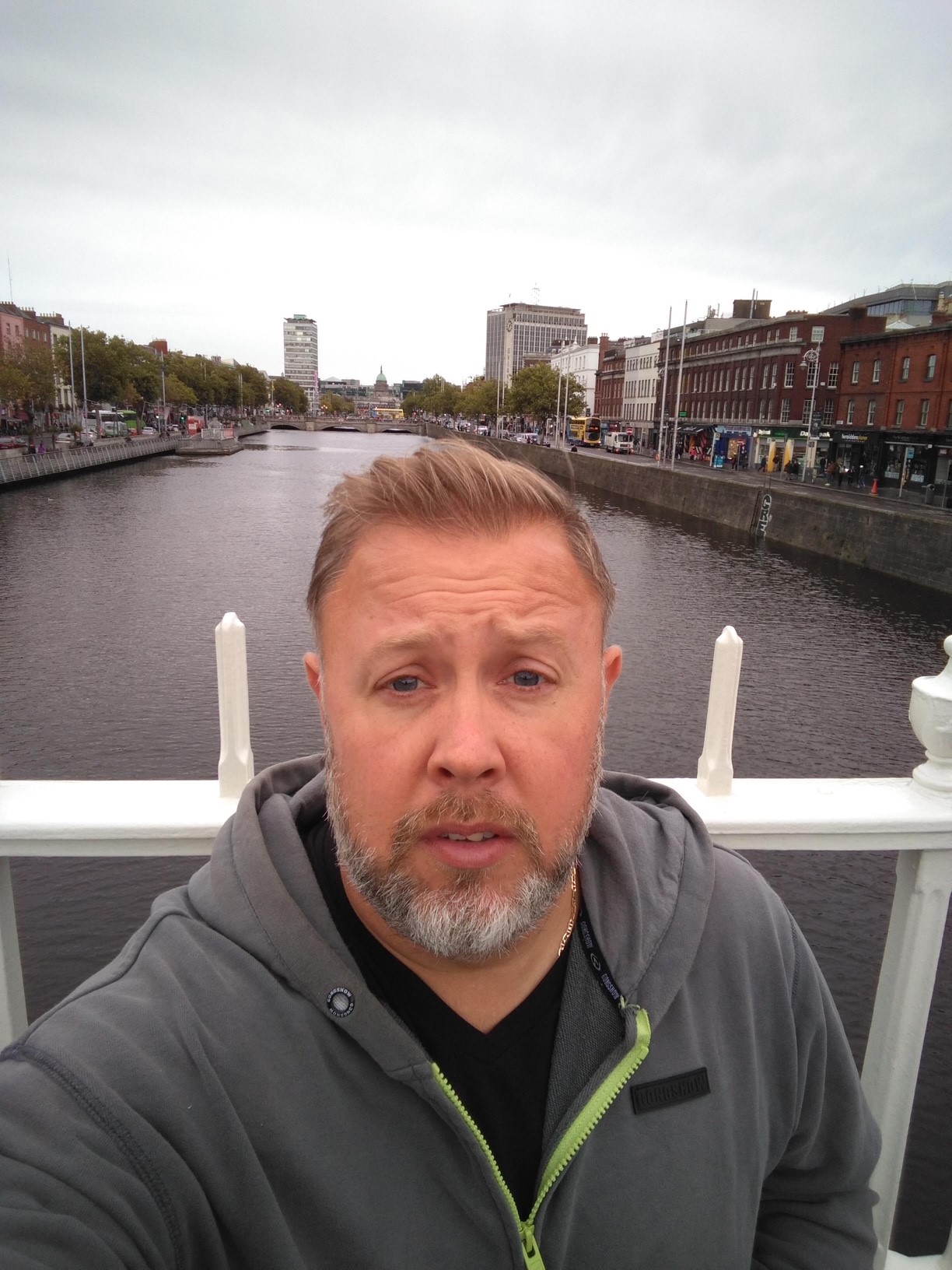
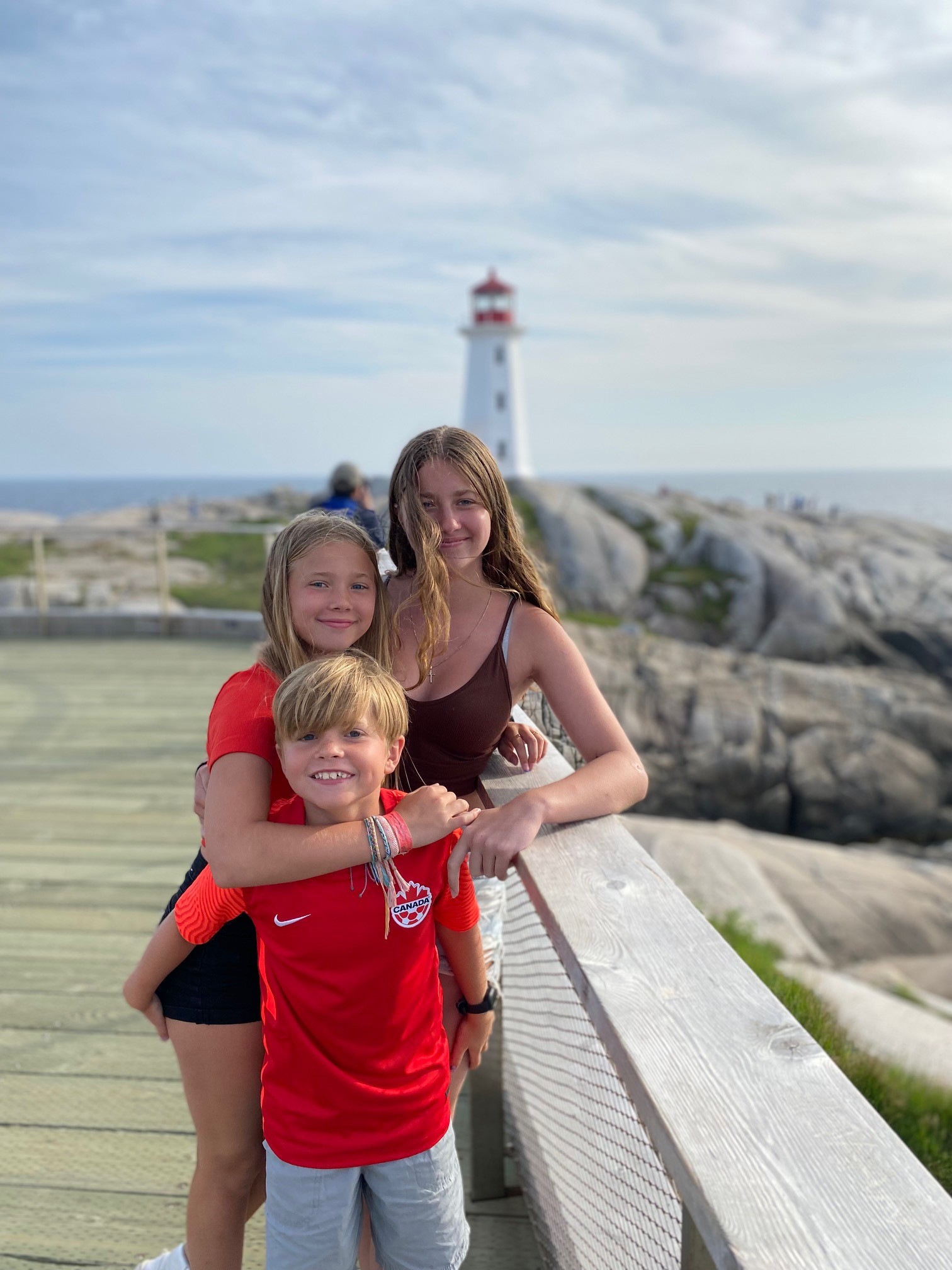
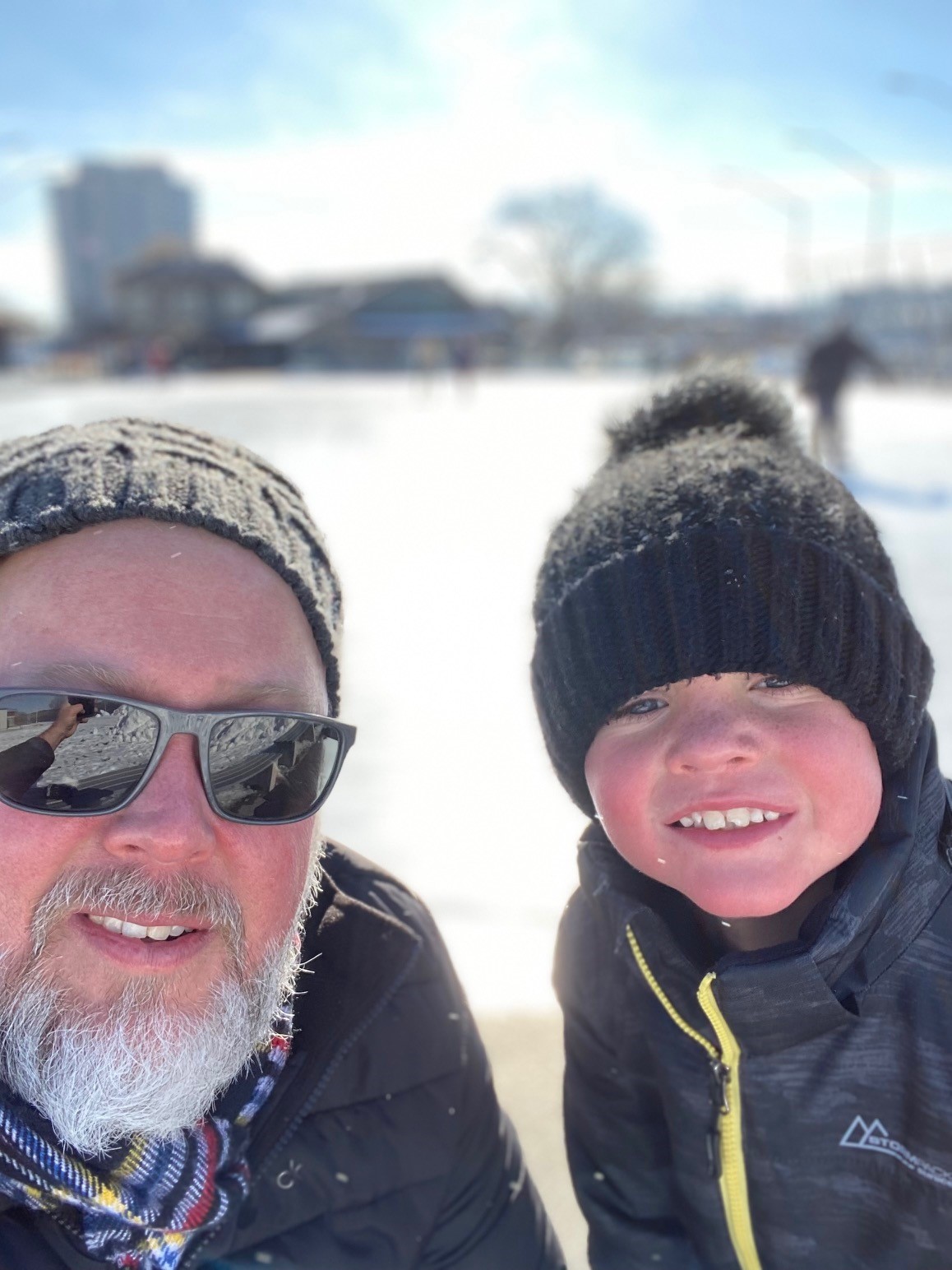
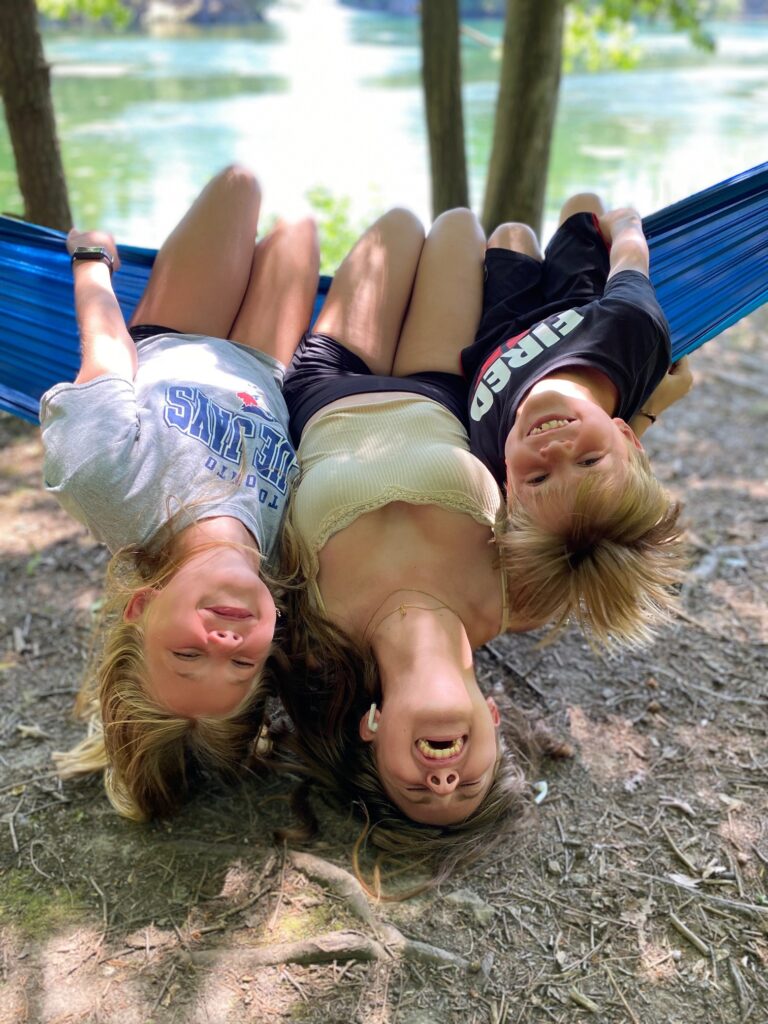
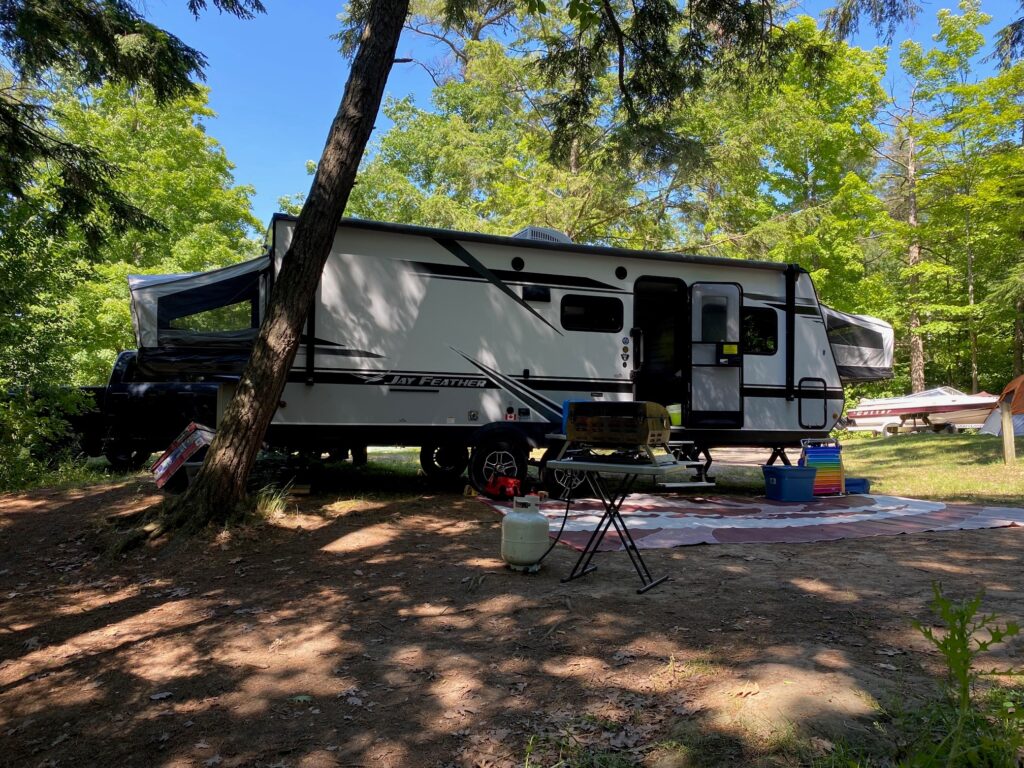