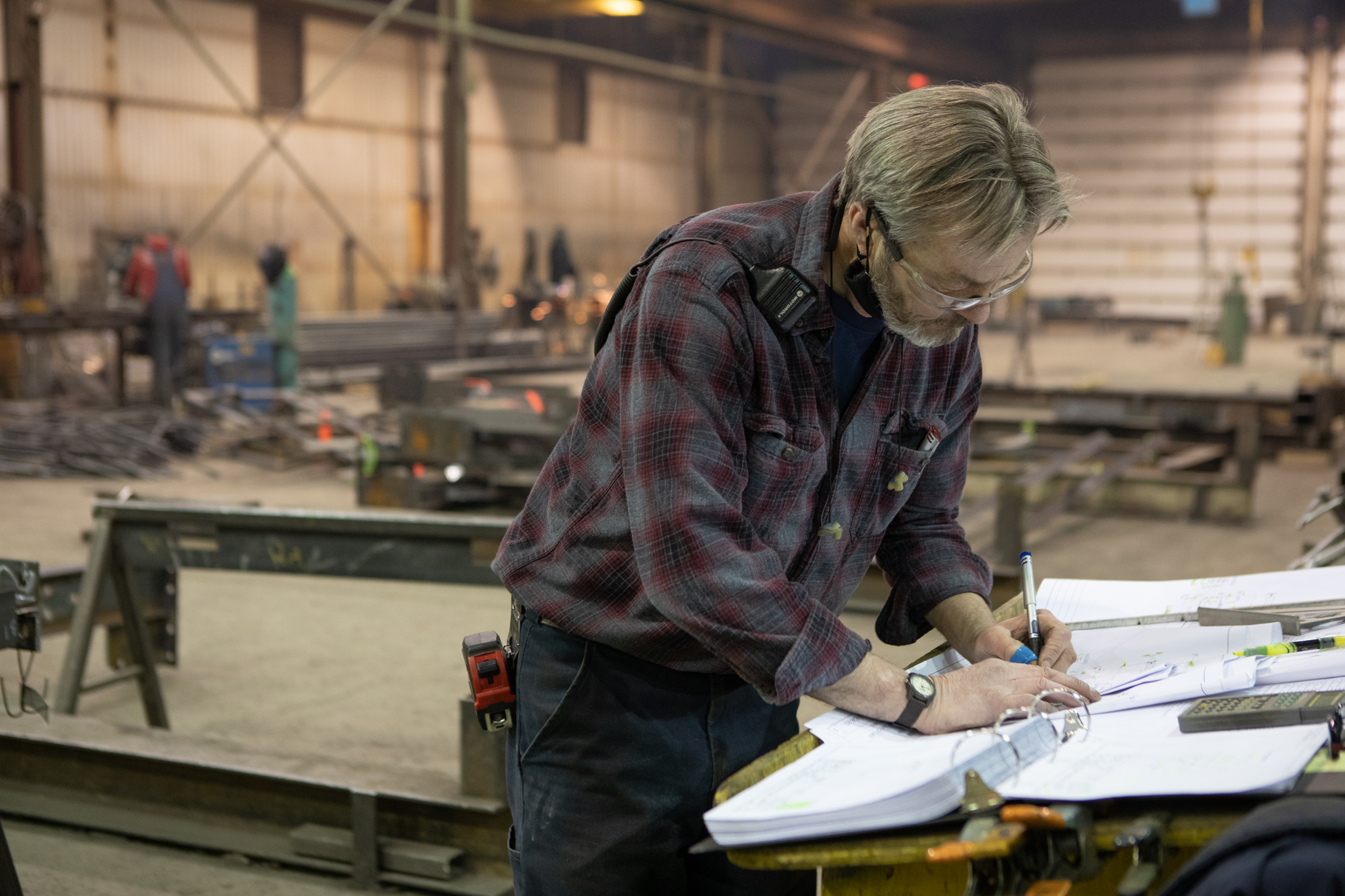
Essential Safety Measures in Bulk Material Handling
Safety is a vital component of bulk material handling. Industry standards and guidelines ensure organizations operating in bulk material handling abide by safe work practices and prioritize protecting their employees.
Safety Standards & Guidelines
Bulk handling operations are held to an incredibly high safety standard and must abide by several rigorous standards and guidelines to ensure the safety of everyone involved.
- OHAS (Occupational Health & Safety)
- MSHA (Mine Safety and Health Administration
- CE (Compliance with goods sold in the EU)
- CSST (Construction Site Safety Technician)
Safety Guarding
With any bulk handling system comes legal requirements, such as machine safety guards that must be complied with in order to operate in a safe manner. The engineering and design of proper machine guarding is just as important as the conveyors themselves. Proper guarding provides optimized safety features to protect workers from fatal accidents related to working near, inspecting, adjusting or maintaining conveyor belts.
A general rule in regards to safeguarding is that equipment must be guarded at accessible pinch points. Pinch points are places where it’s possible for a body part, clothing, or object to get caught between moving machine parts or between moving and stationary machine parts. Such accessible pinch points must be guarded at head, tail, drive, and deflection pulleys of conveyor systems. Proper safety guarding your bulk handling equipment is the law and must be prioritized by both manufactures and operators.
Important Safety Measures to Consider When Working with Conveyors
Conveyors are designed and manufactured specifically for the materials being conveyed. However no matter the size or its contents, there are standardized safety measures all conveyors should be equipped with. All conveyor systems have inherent dangers when in motion. The following standards can reduce risk to workers by following safe work practices during operation and maintenance.
OHAS
- Emergency stop button or pull cord
- Emergency stop cables that extend the entire length of the conveyor so they can be accessed from any location
- Ensure appropriate personnel perform inspections prior to restarting the conveyor after being stopped due to an overload
- Provide guards where conveyors pass over work areas or aisles
- Ensure proper ergonomics of conveyor system in regards to the size and weight of the material being conveyed
MSHA
- Audible and visible warning systems to signal the start of the conveyor
- Practical belt crossing facilities at strategic locations near controls
- Pull cords for emergency stops at strategic locations
- Ensure adequate guarding is installed to prevent contact between workers and moving parts of the conveyor
- Ensure power is disconnected during maintenance and repairs by locking out and tagging out the energy source
- Never attempt to cross a moving conveyor belt except at suitable crossings
It is essential to be able to protect workers while keeping up with production imperatives in bulk material handling. Working with experienced leaders in the bulk handling industry will ensure that equipment is designed and manufactured according to the proper safety standards and guidelines and operates efficiently.
Basic Industrial Design (BID) helps industry move what matters. Our expertise in the design and manufacturing of bulk material handling systems will help you manage bulk material safely, efficiently and responsibly. With nearly 50 years of niche experience, combined with our central location, we are leaders in the bulk material handling industry in eastern North America.