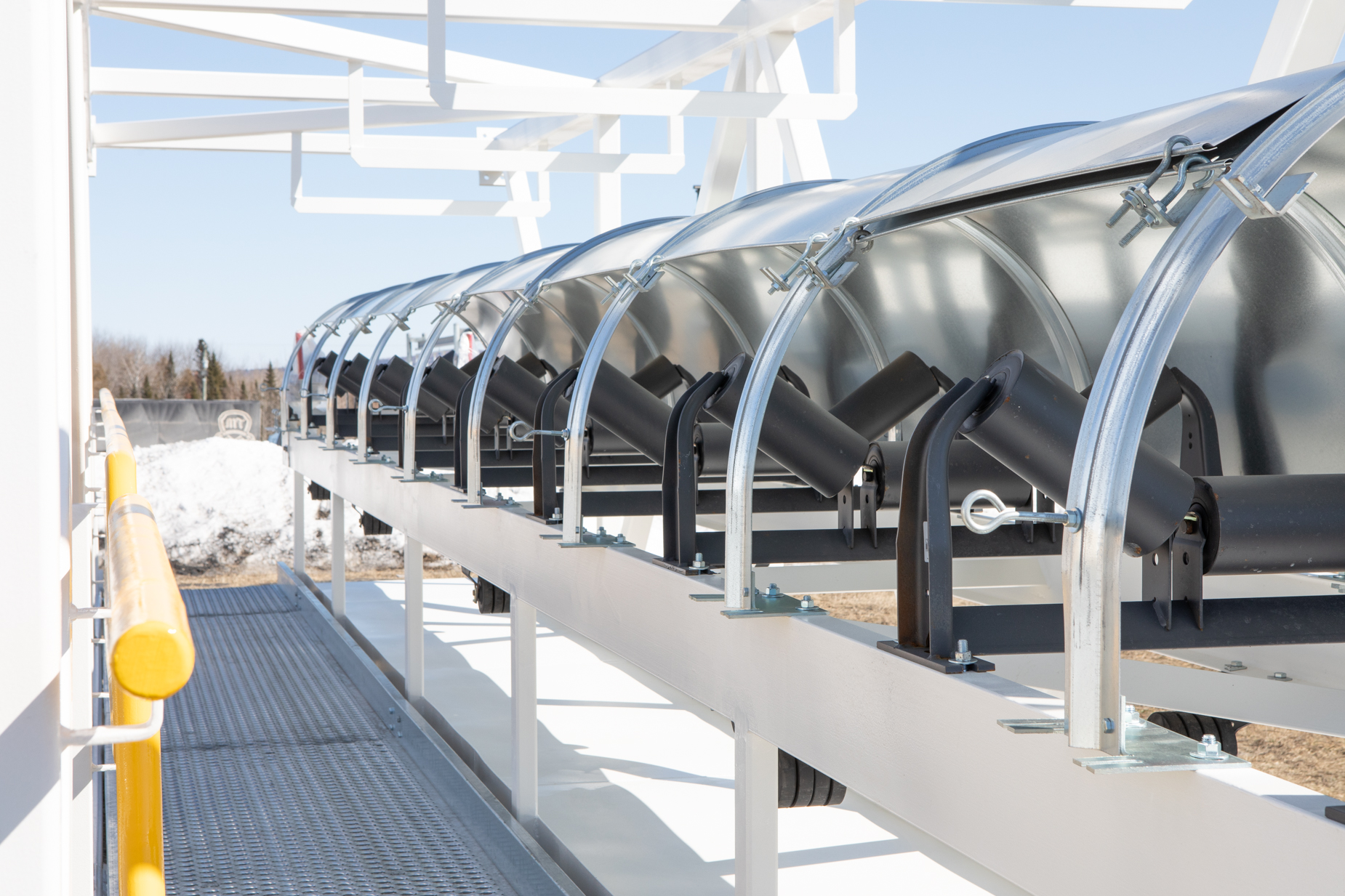
The Backbone of Bulk Material Handling: Conveyor Systems
In the bulk handling industry, conveyors are the most prominent piece of equipment which enables the transport of materials from point A to point B. Conveyors are an essential component across several industries; environmental, energy and power, lumber and wood, metals and mining, oil and gas, pulp and paper, stone, glass and concrete. Depending on the industry, conveyors are strategically designed and manufactured based on the properties of the materials being conveyed and for a wide range of capacities and distances.
Types of Conveyors
Belt Conveyors
Belt conveyors are typically used to convey materials such as salt, ore, grain, sand from mines or pits to processing plants. They are considered to be the most economical of the three conveyor types as belt conveyors are capable of handling high volumes of material at faster speeds and for long distances. Belt conveyors consist of two or more motorized pulleys with a continuous loop of belting material to convey materials.
Screw Chain Conveyors
Screw chain conveyors are known for their versatility as they can withstand a wide variety of free-flowing and non-free-flowing materials and fulfill many different functions. Chain conveyors are typically used for heavier loads and operate by a series of gears connected into a continuous system by the chain.
Pneumatic Conveyors
Pneumatic conveyors are typically designed to convey dry, low-bulk density materials such as sands, cement powder, sugar and wheat using pressure differentials and the flow of compressed air or nitrogen. Materials are enclosed in tubes or pipes and pushed throughout the conveyor by different pressure levels.
Modular Conveyor Systems
Often, conveyor systems are built off-site and require being shipped to production facilities from afar. Considering the significant size of such systems, their rigidity can pose problems. Additionally, inflexible equipment can often result in deficiencies such as maintenance disruptions and logjams leading to costly repairs and replacement. Modular conveyor systems allow for several benefits, can improve process flow and provide companies with competitive advantages.
Benefits of Modular Conveyor Systems:
- Flexible shipping solutions
- Ease of construction, fabrication, installation
- Allow for many types of configuration
- Shorter assembly time
- Expedite maintenance
- Facilitate system integration
- Enhance quality assurance
- Reduce labour and replacement costs
Conveyor Maintenance Should Not Be An Afterthought
Careful thought in the design process has a direct correlation to the ease of maintenance for your conveyor system. It’s crucial to consider the technician who is responsible for maintaining the system, so they’re provided with easy and safe access to equipment and can perform maintenance in a timely manner. It’s also important to ensure the components in your conveyor system are carefully and correctly designed and selected. High-quality design and supplies provide for easy maintenance practices, enable trouble-free operations and achieve maximum uptime.
Preventative Conveyor Maintenance:
- Ensure system is properly installed to ensure long term performance and reliability
- Follow a comprehensive maintenance plan
- Check chain and belt tension regularly
- Monitor belt tracking closely
- Clean conveyors regularly
- Perform conveyor system audit and documentation
Proper conveyor maintenance plays an important role in the systems reliability, safety, and overall environmental conditions of the conveyor and surrounding facilities.
Basic Industrial Design (BID) helps industry move what matters. Our expertise in the design and manufacturing of bulk material handling systems will help you manage bulk material safely, efficiently and responsibly. With nearly 50 years of niche experience, combined with our central location, we are leaders in the bulk material handling industry in eastern North America.